Professionalism
「オール住重」で取り組むトラブル解決
~ トラブルを改善の契機に変える、
一歩踏み込んだ装置安定稼働への取り組み ~
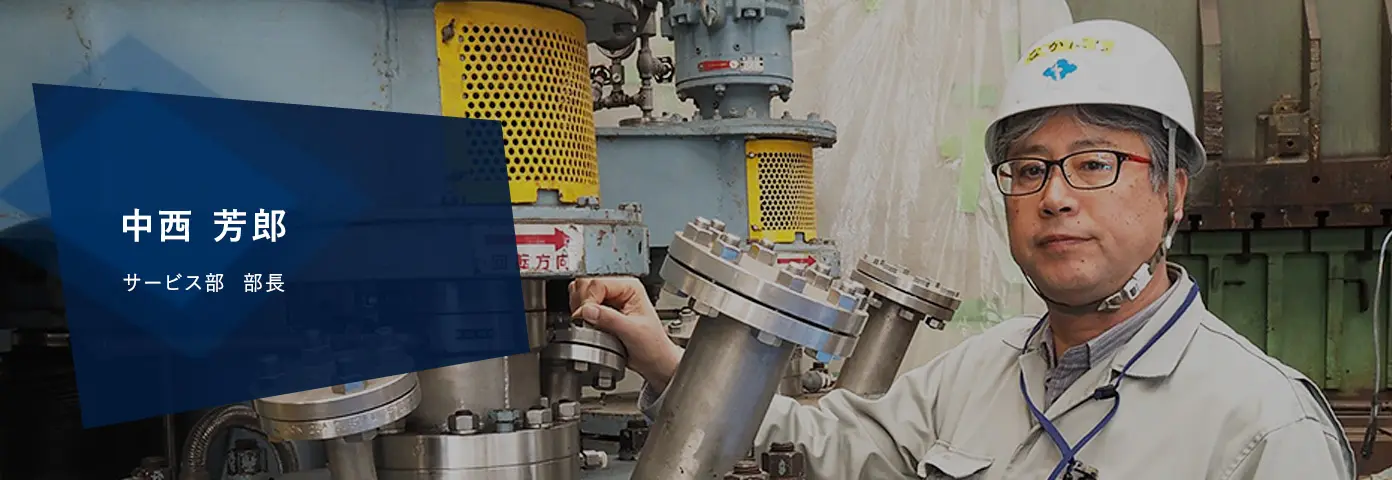
アフターサービス After Service
世界各地で運転されている当社の撹拌槽。 お客様に納入した後の装置の安定稼働を支えるプロフェッショナルの一人が、 当社製造部の中西です。
お客様の製造プロセスを支える撹拌装置。 そのトラブル解決に取り組み続ける中西に、 これまでに経験した装置不具合解決のエピソードを聞きました。 トラブルをきっかけに「お客様の装置をさらに進化させる」という、 その徹底したこだわりとは?
撹拌装置について、 どのような体制でトラブル対応に取り組んでいるのでしょうか。
当社は、 MAXBLEND®やSUPERBLEND®といった高性能撹拌翼はもちろん、 撹拌装置の「釜」、 つまり圧力容器の事業も長年に渡って手がけています。 また、 装置を駆動するモータや減速機もグループ内の企業が手がけていますから、 装置全体の開発から引き渡し後に発生したトラブル解決までオールマイティで対応することが可能です。 この「グループとして撹拌装置に関するあらゆる知見を持っている」ということが、 翼や釜専業のメーカーさんとの違いであり、 それが当社の強みと言えます。
さらに、 住友重機械の技術研究所や大学とも連携することで、 高度な化学分析によるトラブル原因の追求も可能です。
「住重の強みである、 グループの力を結集したオールマイティさ」が、 トラブル対応にも生きているということですね。 では、 早速ですが具体的なトラブル解決事例について話を聞かせてください。
トラブル解決事例① ステンレスの応力腐食割れによる内容物漏れ
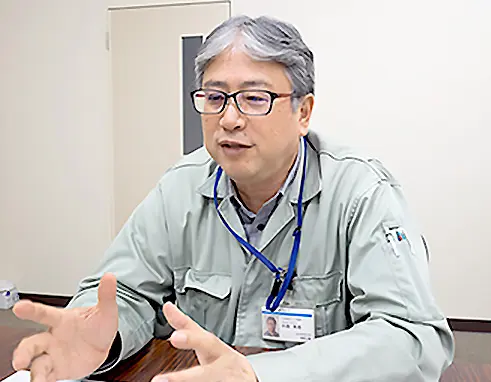
まずは、 2013年に経験しました化学メーカーA社さんの事例からお話しましょう。
応力腐食割れ、 SCC(Stress Corrosion
Cracking)と言いますが、 これは化学メーカーさんが非常に神経をつかわれるトラブルですね。 発生条件が限られているため簡単には発生しないものですが、 使用する原料によっては急激に腐食割れが進み、 危険な物質漏れが起こるリスクの高いものです。
どういう発生条件なのでしょうか。
一般的に、 材料因子(ステンレス)、 応力因子(高温による引張応力)、 環境因子(今回は塩素)が関係しており、 3つの条件が重なって発生するものです。 お客様から漏れがあったという連絡を受けて現場に急行したのですが、 我々も最初は原因が応力腐食割れだと分かりませんでした。
しかしお客様にしてみれば、 なぜ運転を開始してわずか4,5年で、 極厚の鋼材を貫通して漏れが起こったのか、 大変心配されていました。 まずは運転再開を最優先に、 補修工事として該当部材を全て取り替えさせていただきました。
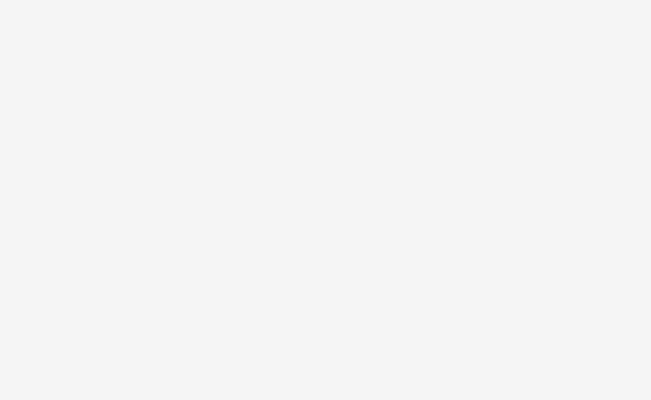
そして調査開始ですね。
はい。 原因が分からないと対処法が定まらないため、 割れを起こした箇所を切り取り、 当社グループの研究所に持ち込むことにしました。
ステンレス組織のEPMA(Electron
Probe Micro-Analyzer)分析を行ったところ、 応力腐食割れに特徴的な高濃度塩素を割れ部に発見することができました。
しかし、 ここで大きな疑問点が浮かび上がります。 トラブルが起こったプロセスでは、 そもそも塩素を含む原料は使用されていなかったのです。 そこで、 お客様と協力しながら、 「どうして応力腐食割れが発生したのか」根気強く原因を追求していくことになりました。 すると、 撹拌槽を洗浄する際に用いる薬剤が怪しいことが分かってきました。 この薬剤にはごく微量の塩素が含まれていたのです。
最終的に3ヶ月の調査を経て、 薬剤の洗い流しが充分ではなかったために撹拌槽下部のノズルの液溜まりに僅かな塩素が残留し、 温度の上昇・下降を経るうちに徐々に濃縮され、 応力腐食割れに至ったと判明しました。
お客様には、 塩素濃縮が進行しないように容器をメンテナンスすることをご提案させていただき、 現在は安定稼働しています。
根気強く調査していくことで、 想像もしていなかったような原因が判明したんですね。
はい。 30年以上この業界で働いていますが、 未だに知らない世界が沢山あることに気付かされますね。 日々、 勉強だと思って取り組んでいます。
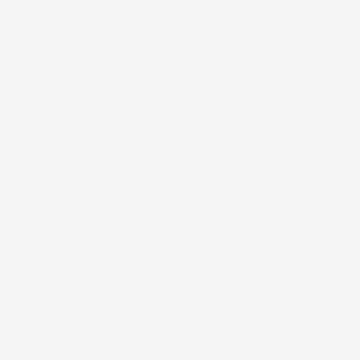
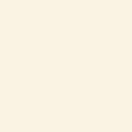
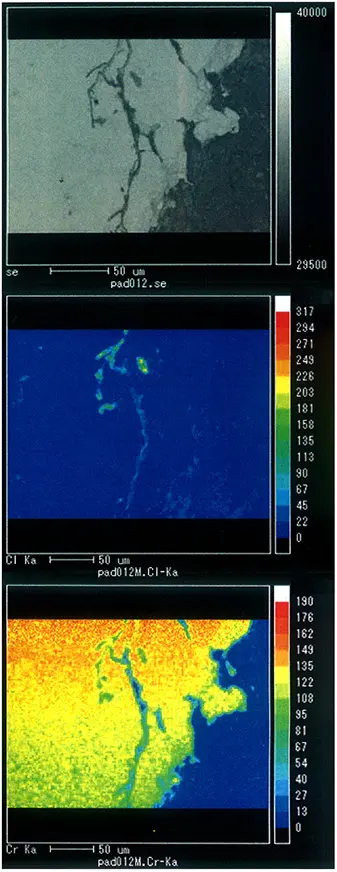
SCC発生と塩素濃度の関係
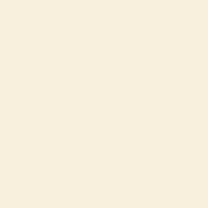
トラブル解決事例② 大型減速機のベアリング損傷
もう一つご紹介したいのが、 化学メーカーB社さんの中国工場に納品した撹拌槽の事例です。
非常に大型の撹拌装置で、 駆動用モータ容量が710kWもある大型の減速機が装着されていました。 ところが、 かなり頑丈なはずの減速機中間軸が出力軸ベアリングを起因として損傷してしまった、 というトラブルです。 Φ300mmもある軸が、 運転を始めてわずか一年半で損傷してしまったということで、 お客様はもちろんですが我々も大変驚きました。
標準品であれば過去のトラブルから原因をある程度類推できるのですが、 ここまでの大きさの減速機になると特注品になってしまいますから、 原因を突き止めるのは大変でした。 損傷した該当部品を国内に持ち帰り、 製造にあたったグループ企業の協力を得ながら、 組織分析を行ったり断面を見てみたりと試行錯誤を繰り返しました。 最終的に大学の先生に分析結果を見て頂き、 損傷に至ったメカニズムをご教示いただくことで、 ようやく原因が判明しました。
原因ですが、 実は減速機の潤滑油に、 1mmに満たない大きさの異物が混入しており、 それがベアリングに噛み込まれ、 圧痕が発生し、 材料内部の応力状態に不均一な領域が生じて疲労破壊へと至ったことが判りました。 お客様にはSEM(Scanning Electron Microscope)の分析画像をご提示し、 金属組織が疲労で破断していることを説明して、 メンテナンスで潤滑油を添加する際には異物が混入しない様に目の細かいフィルターを採用する等の異物混入防止処置をとっていただくように提案させていただきました。
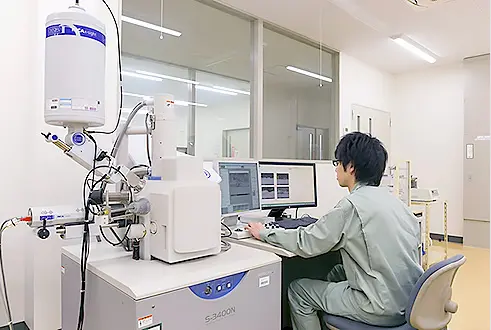
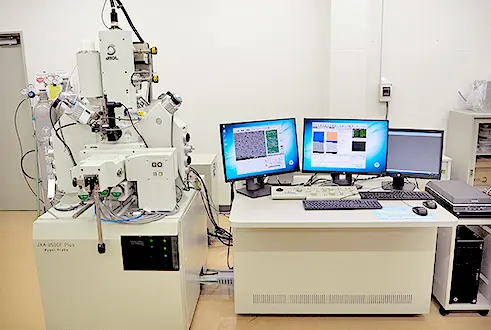
先程の事例は3ヶ月で解決しましたが、 今回はどれくらいの期間がかかったのでしょうか。
こちらのトラブルも、 まずは運転を再開していただくためにすぐに軸を交換し、 その上で調査に着手しました。 しかし運転開始から間もない一年半で発生したトラブルだったため、 お客様は再発の可能性を非常に気にされていました。 そこで、 最大限スピーディーに取り組み、 海外でのトラブルながら2ヶ月程で解決することができました。
事例①も②も、 科学捜査のような精緻なアプローチですね。
言われてみれば、 科学捜査そのものですね(笑)
何事も壊れ始めの起点となる部分があります。 その起点を、 どこまでも突き詰めて調べていくことが大事です。
当社のグループの横須賀や新居浜の研究所は、 重工系のメーカーとして材料化学分野でも大きな強みがあります。
ですから、 成分分析から組織のマクロ観察までスピーディーな対応ができるんですね。 国内の大学とのリレーションもありますから、 こうした分析的なアプローチでの問題解決は競合企業さんと比較すると大きな強みと言えると思います。
また、 当社は過去に原子力容器を手がけていましたから、 溶接系や材料系のトラブル対応についてはそのノウハウの蓄積も豊富にあり、 今も非常に得意としています。
トラブルを解決したら、装置の運転が安定し、メンテナンスコストが下がった…
そんな提案を心がけています。
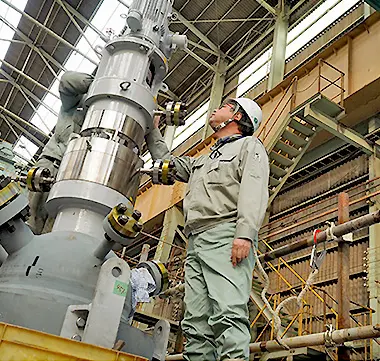
こういった科学的なアプローチ以外に、 日頃心がけていることはなんですか?
様々なトラブル対応を経験していますが、 当社が手がける撹拌装置は基本的に全てオーダーメイドですから、 発生するトラブルもその原因も千差万別です。 先ほども言いましたが、 標準品であれば対処法もある程度見当がつきますが、 うちの場合はそうもいきません。 例えば「ジャケットからの熱媒の漏れ」というトラブルひとつとっても、 やはりまずはお客様の所に行き、 実際に見てみないと状況が分からない。 また、 プロセスが止まる期間が長ければ長いほどお客様の損失も拡大していくわけですから、 なるべく早く運転を復旧させるということも必要です。 そういう意味でも、 急ぎ現場に行って、 現物を見て、 現実を知る、 という「三現主義」は大切ですね。
もう一つは、 トラブルの原因を取り去るだけでなく、 お客様の装置に特有の運転条件に合わせた提案をすることを心がけています。 お客様の機器に対して最適なカスタマイズを見つけ出すことで、 メンテンナンスが楽になったり、 運用コストが低くなったり、 という一歩踏み込んだ解決が可能です。 トラブルを機会ととらえて、 お客様の装置の寿命を長期化させる、 ということですね。
トラブルを契機として安定運転の為のリスクを無くすというのは、 非常に前向きな考え方ですね。
最後になりますが、 この仕事の醍醐味は何だと思いますか?
装置が停止し生産が止まっている状況においては、 トラブルの原因がたとえ当社ではなくても我々が現場に駆けつけるなり「どうなっているんだ」とお叱りを受けることもよくあります。
しかしどんな状況でも、 お客様のために一生懸命ベストを尽くして問題解決に取り組む。 そしてできるだけ早い解決を模索する。 場合によっては数か月かかることもありますが、 精一杯やる。 お客様に寄り添い、 お客様ごとにオーダーメイドの解決策を考えて、 そしてお客様に喜んでいただく。 その経験があるからこそ、 この仕事を続けられていますし、 そこに、 この仕事の醍醐味があると思います。 一生懸命やれば、 喜びもひとしお、 ということですね。 今後も、 そんな「やっぱり住重さんだね」と言っていただけるような問題解決を心掛けていければと考えています。
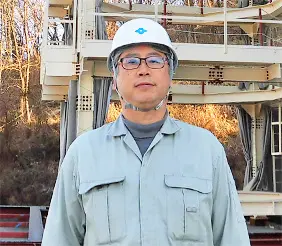
当社のプロフェッショナル
中西 芳郎
住友重機械プロセス機器株式会
サービス部 部長
1982年入社。
学生時代は機械工学を専攻。 設計、 技術、 工事、 品質管理など様々な部署での長年のキャリアを通して、 石油掘削リグや海洋構造物、 本州四国連絡橋のケーソン、 橋梁、 コークス炉機械、 そして撹拌装置と多種多様な機械構造物を取り扱う。
現在は製造部の部長として、 日本国内はもちろん中国、 韓国、 タイなどアジア圏を駆け回る日々。