撹拌講座 貴方の知らない撹拌の世界
- HOME
- 製品・ソリューション
- 撹拌槽
- 撹拌講座
- 実践コース その7:水添槽では運転中に主役が交代する?
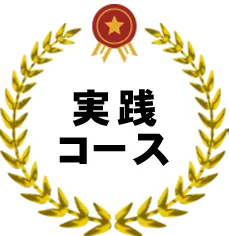
その7
水添槽では運転中に主役が交代する?
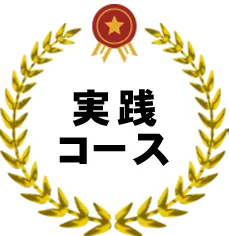
前回、 ガス吸収槽の計画段階では、 ①通気条件の事前把握と②運転方法の確認次第で、 選定されるモータ容量に大きな差が生じることをお伝えしました。
今回は、 化学企業の生産スタッフが「製品の付加価値向上のために、 どのような改善を進めているのか?」 また、 その際に生産の道具として使用される「ガス吸収槽に要求される主要機能と性能には、 どのようなものがあるのか?」に関してお話しましょう。
化学プラントの中でガス吸収操作を行うプロセスは多々ありますが、 本編では前段の重合槽からの製品を受けて、 後段で水素を添加するガス吸収槽(以下、 水添槽)の事例を紹介します。
図1は、 一般的な水素化ポリマーの製造フローです。 原料モノマーに重合触媒を加えてポリマーを製造し、 さらに水素化触媒と水素を加えて水素化ポリマーを製造しています。
通常、 重合を行う撹拌槽を「重合槽」、 水素化を行う撹拌槽を「水添槽」といい、 各々バッチ式撹拌槽の2缶直列で運転されます。
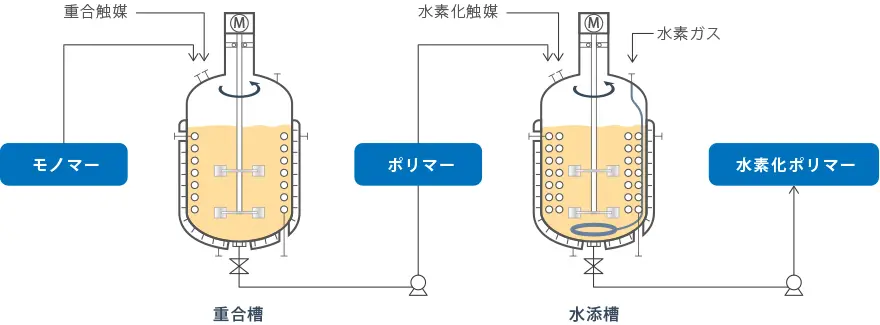
ケーススタディ:
とある撹拌装置メーカーのオフィスにて
さてさて、 装置メーカーのいつもの二人がこの「水添槽」について、 何やら話をしています。
-
ブレンディ君 もともと危険物の多い化学工場で、何故リスクの高い水素を高圧下で添加させる 必要があるんでしょうか?その目的って何でしょう?
-
ウエダ所長 顧客からは、製品の品質を安定させるためと聞いたことがあるが…
-
品質って、具体的には何ですか?
-
ううぅ~、実は詳しくは分からんのじゃ…
二人とも装置メーカー社員として、 化学会社の皆さんと日々、 お付き合いを重ねているものの、 その意図までは、 なかなか具体的には把握できていないものですね。 莫大な労力と期間を費やしてでも、 高価な水添設備を必要とする化学会社の本当の意図(こうなって欲しい)は、 どこにあるのでしょうか?
何故、人は樹脂や油脂を水素化したくなるのか?
水素化は、 ゴム、 エラストマー、 プラスチック、 バターおよびマーガリン等の樹脂や食用油脂の製造現場で古くからみられる工程です。
何故、 人は自社製品に水素を添加させたくなるのでしょうか? 一般的な回答は、 前述のウエダ所長の言葉通り「製品中に水素が結合すると、 その品質が向上するから」なのです。
この「品質向上」に関する具体例として、 ここでは、 自動車エンジン内部にあるタイミングベルトの事例を紹介します。
タイミングベルトとは、 エンジンを動かすのに必要なパーツの一つで、 もし、 タイミングベルトが切れると、 エンジンの動きが乱れ、 エンジンに深刻な影響を与えてしまうこともあります。
下の写真が、 自動車用タイミングベルトです。
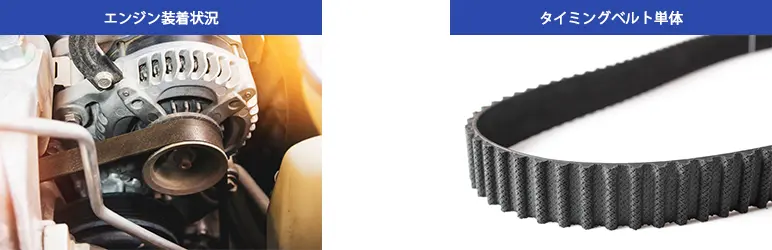
1970年代に入り、 自動車の排ガス&燃費規制への対策で、 電子燃料噴射方式の採用と自動車の小型軽量化が急速に進みました。 その結果、 当時のエンジンルーム内のゴム製タイミングベルトへも新たな厳しい品質が要求される状況となりました。
自動車用タイミングベルトの交換時期は、 購入から10年または走行距離10万km程度と言われていましたが、 エンジンルームのコンパクト化と車内電気計装品等の増加に伴い、 ベルト素材(合成ゴム)の耐熱性や耐薬品性への要求品質が急激に高まりました。 また、 ベルトがエンジンの中に組み込まれており、 外部からそのベルト自体の損傷状態を検査・確認することが難しいパーツであるため、 安全面からも素材自体の耐久性向上が待ったなしの状況でした。 従来では両立し難い、 耐熱性と化学的安定性の両面機能を持つ合成ゴムの開発が必要となったのです。
ここで、 重合槽にて製造された合成ゴム(ニトリルゴム)を、 水素化処理をしないでそのまま使用した場合(図3)と、 水素化処理をした場合(図4)での分子構造を比較してみましょう。
水素化処理をしない場合は、 炭素二重結合部分が外部環境中の水酸化イオン(OH)からの攻撃を受けて、 容易に手をつないでしまうことから、 酸化劣化のリスクが高くなります。 一方、 水素化処理をした場合は、 炭素二重結合が水素で置き換わり、 安定した一重結合となることで、 外部環境からの攻撃に対する製品の耐久性が向上するのです。
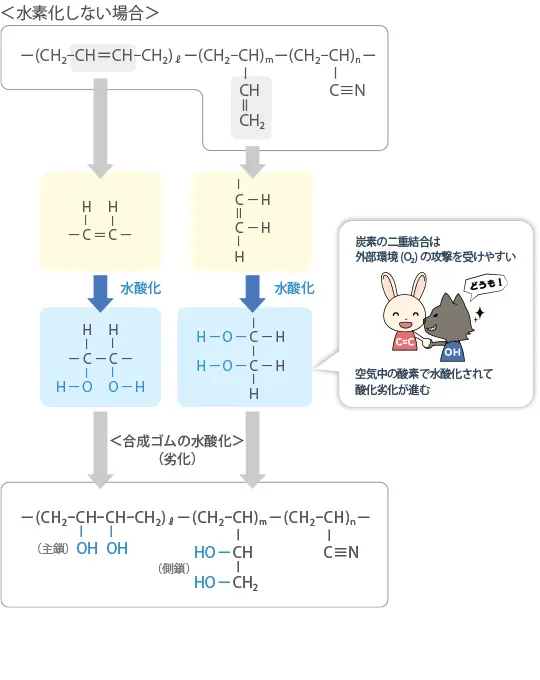
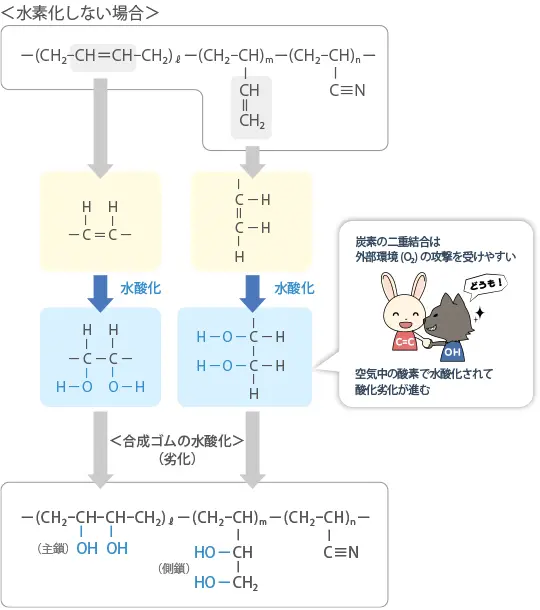
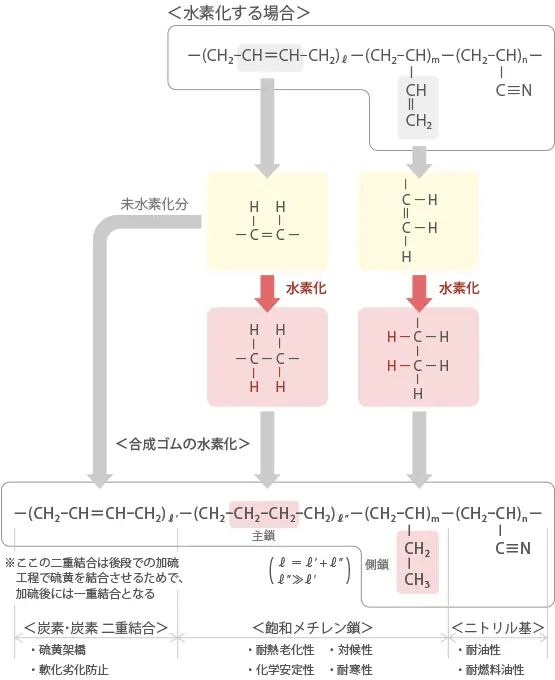
品質向上のためのニトリルゴム分子構造変更の設計メカニズムは以下となります。
- ①高分子製品の分子構造には、 炭素・炭素の二重結合を有する箇所がたくさんある。
- ②この炭素二重結合の部分は、 結合している手を外して他の原子と結びつきやすい「活発な反応性基」であり、 酸素等の外部環境からの攻撃で水酸化されることで、 長期使用下では酸化劣化等で耐熱性や化学安定性が低下してしまうリスクがある。
- ③そこで水素化操作により、 この二重結合箇所に水素を結合させ、 ポリマー中の炭素二重結合(反応性基)の数を大幅に減少させることで、 長期の使用に耐えうる安定した品質を確保できるようになる。
-
世の中の流れを受けて、自動車会社はタイミングベルトの寿命を確保する必要があった。そして、そのニーズを受けた化学会社は、タイミングベルトの原料である合成ゴムの品質を強化するため「水素化」を行い、その手段を実行するための道具が水添槽だった、というワケだな。
-
そうか、僕らのお客さんにも、その先にお客さんがいるのか。
-
顧客の顧客を知って、初めて“顧客の立場に立てる!”ということだね。
いかなる業界の、 いかなる企業においても、 顧客の意図(WHAT)を知ることはとても大事です。 なぜならば、 そのWHATは「顧客の顧客」にあたる世の中のメガトレンドからの要求項目であるからです。 逆に言えば、 そのメガトレンドが変われば、 自動車会社も変わり、 化学会社も変わり、 その装置メーカーへの要求も変わっていくということです。 変化の激しい現代で生き残れる者は、 大きくて強い者ではなく、 変化に気づいて、 静かに身体を適応できる者なのです。
化学会社であれ、 装置メーカーであれ、 そこの技術屋は顧客の投資理由など気にせずに、 自社製品に要求される機能とその性能向上に集中すれば良いと言う声もあります。 しかし、 自社製品の付加価値を上げるという顧客ニーズは、 実は顧客の顧客から要求されたニーズであることが多いのです。
対象市場の十分な顧客ニーズを把握していない商品改良や新規開発などは技術屋の自己満足でしかありません。
いろんな場面で「顧客の立場で考えろ!」の声を聴きますよね。 でも、 具体的にどんな行動を取れば、 そうなれるのでしょうか。 それは、 顧客の声を真摯に受け止めて、 何故、 何故、 何故を重ねることで、 顧客の本音の「WHAT」が理解でき、 顧客の立場に立った発想が可能になるのだと想っています。
今回は、 自動車用タイミングベルトの事例を紹介しましたが、 水素化による品質向上事例だけを取り上げても、 以下表1のように多数存在します。 これら要求品質の一つ一つに、 サプライチェーンが一体となって付加価値向上のための取組を行ってきた数多くの企業努力が詰まっており、 国際競争力を有する企業というのは、 メガトレンドのニーズ変化に迅速に対応し、 自社製品の機能を強化し続けているのです。
製品分 | 用 途 | 要求品質 |
---|---|---|
特殊合成ゴム | 車の燃料ホール、オイルシール、タイミングベルト | 耐熱性、耐油性、耐薬品性 |
透明樹脂 | 光学レンズ、光ファイバー、プリズム | 形状安定性(耐吸湿性)、耐熱性、加工性 |
石油樹脂 | 粘・接着剤(紙おむつ、車用電気部品) | 低臭気、黄色みの白色化 |
食用樹脂 | マーガリン、フライ用食用油、ハードバター | 融点上昇、酸化安定性 |
テレフタル酸(精製) | 繊維(ポリエステル樹脂)の原料 | 着色(黄色)成分の除去 |
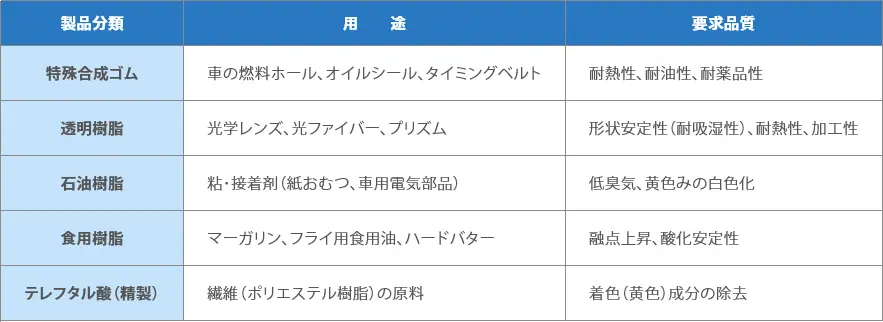
<出典>高分子製造プロセスのアセスメント19 水素化によるポリマーの製造
(反応工学研究会 研究レポート 1998年)
水添槽に要求される機能は、運転現場のオペレータに聴け!
化学会社が何故、 自社製品をわざわざ水素化するのか、 その理由がなんとなく理解できましたね。
それでは、 水素化を行う道具としての水添槽に要求される機能には、 どんなものがあるのでしょうか? 通気撹拌性能への影響因子と言えば、 撹拌の教科書を見ると、 撹拌強さPvとガス空塔速度Ugの2因子が出てきます。 でも、 この2因子だけで生産性の高い運転ができるのでしょうか?
現場でガス吸収槽を運転しているオペレータからは、 前述の2因子(PvとUg)以外にも、 装置自体が保有する除熱機能や自由界面からのガス巻き込み機能が重要になる場合も多いとの声を聞きます。 ただし、 この手の話を断片的に聞いてしまうと、 設備計画時に「除熱性能が大事だから、 たくさん伝熱コイル入れよう」とか「バッフル無しで液面に大きな渦を作り、 その自由界面からガスを巻き込もう」などと、 現場での運転状況を詳細に確認せずに短絡的に判断してしまうリスクが高まります。
ここで、 本撹拌講座の基礎編その2を思い出して下さい。 撹拌槽の中は、 混合、 反応、 伝熱、 吸収等の、 いろんな単位操作のオンパレードだ!とお伝えしましたね。
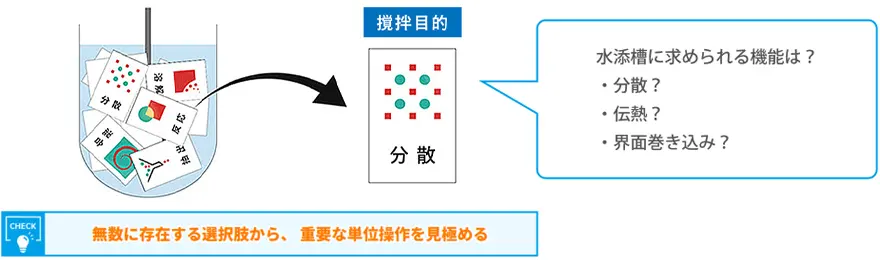
今回は、 水添槽の内部流体が反応の進行とともにどのような状況になっており、 反応を推し進める律速機能が、 どう変化しているかを丁寧に説明します。 本編を理解していただくことで、 目をつぶっていても水添槽内の状況変化が瞼の裏でイメージできる様になれば幸いです。
では、 一般的によく見られる「反応時間と転化率」のグラフから、 水添槽の内部で何が起こっているのかを読み解いていきましょう。
水添槽では、水素化反応の進行により、3人の機能主役が登場する。
図5に水添槽の反応率(水素吸収率)のトレンドを示します。 一般的には、 前半が除熱律速、 後半が液表面からのガス巻き込み律速と言われていますが、 今回は、 もう少し詳細に、 横軸の反応時間をゾーン①から③までの3区間に分けて説明します。
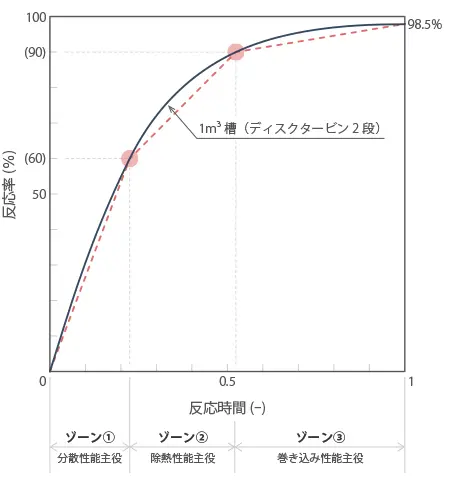
<ゾーン①>
ガスの分散性能が重要。運転温度に到達するまで、反応熱は母液の温度上昇に使われる。
<ゾーン②>
上限液温キープで最大除熱能力で運転。除熱不足時は、水素供給を絞る必要があるので伝熱律速。
<ゾーン③>
反応速度低下で缶内圧力が増大。上限圧力キープで、水素供給は、液界面水素の再巻き込み分のみ可能。
<ゾーン①>撹拌によるガス分散性能が主役のゾーン(物質移動律速)
この領域では、 液中に溶解した水素イオンが結合できる液側の二重結合箇所が多数存在するので、 翼回転数や通気量を出来るだけ増大させて、 ガス吸収速度を最大限に高めることが可能なゾーンです。
反応の進行とともに系内で発生する反応熱は、 ジャケットやコイル等での除熱能力分が除去され、 それ以上の発熱分は、 最大運転温度までは液温自体の昇温に利用されます。 つまり、 本ゾーンは、 常温から最大運転温度までの区間で槽内液温を見ながら、 装置の除熱能力分と液温上昇の熱量分の合計で反応速度を制御可能なゾーンと言えます。
ここでは、 装置が保有する除熱性能よりも少ない発熱量で運転することは、 無駄に運転時間を長くしてしまうことになるので、 吸収速度を上げて除熱性能ギリギリの大きな反応速度で運転できるように、 撹拌強度と空塔速度を上げる操作が必要なのです。 よって、 主役は物質移動速度となります。
以前、 ある水添槽の計画時に「液自由界面積を増大させれば、 気相部のガスを液中へ巻き込む面積が増える。 よって、 槽内のバッフルを外して、 大きな深いボルテックスが形成される運転条件を選定したい。」という意見がありました。 しかし、 現実には図6の写真の通り、 バッフル無し条件では、 回転数を上げてボルテックスの深さを翼高さ付近まで増大させても、 槽内の流れは周方向の旋回流のみとなり、 槽底から供給されるガスの分散や液面からのガス巻き込みは期待できません。
その理由を図7のイラストにて説明しましょう。 ボルテックスの有無により、 単位液量当たりの液自由界面積(A/V)は、 前述の通り確かに増大します。 しかし、 大きなボルテックスが形成している現象は、 イラストからも分かる通り、 撹拌軸付近に固体的回転部(撹拌翼と液の周速が同じになる液循環の無い筒状の領域)が発生していることを意味しており、 ガス分散や巻き込み等の機能を発揮できない状況となるのです。 図8の如く、 ガスの分散・微細化や液自由界面からの巻き込み機能には、 バッフル付きでの強撹拌条件が必要と言えるのです。
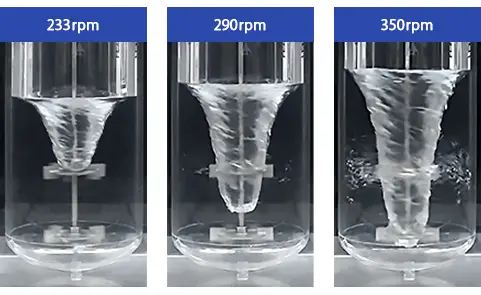
(4枚タービン翼2段)
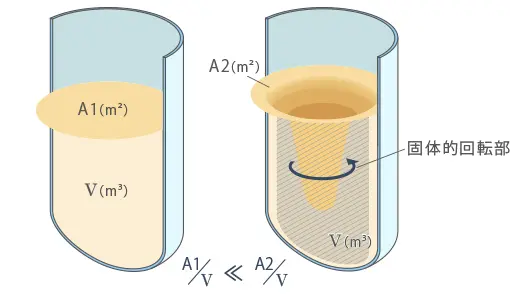
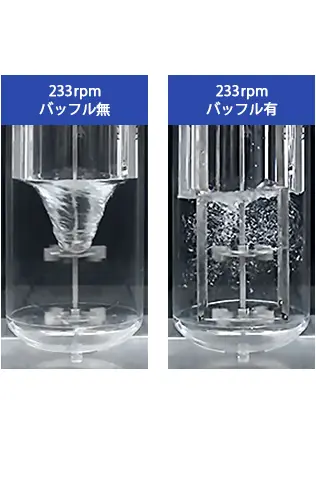
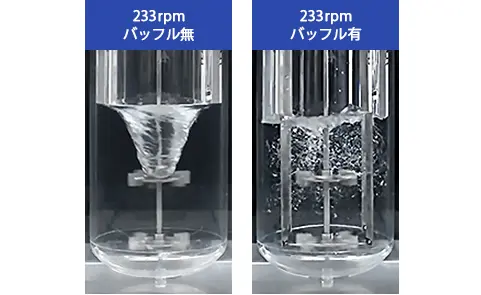
(4枚タービン翼2段)
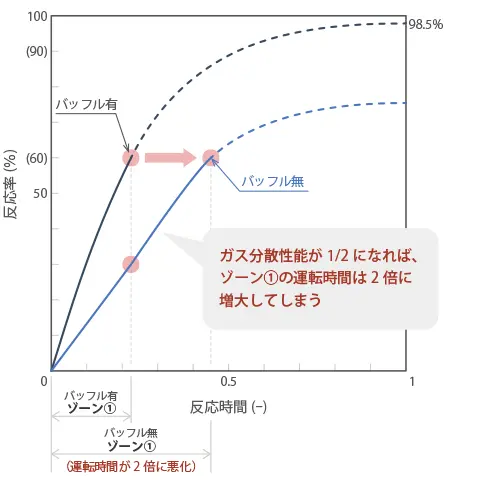
もし、 ゾーン①でのガス吸収性能が半分に低下した場合、 図9の通り、 同ゾーンの運転時間が2倍に延びることになるのです。 これはゾーン②にもつながる話ですが、 一般的に前半が伝熱律速と言われる背景には、 撹拌翼やバッフル等の設計が適切に行われており、 供給ガスの分散・微細化性能が十分に高く、 反応熱の除熱が不足する位にガス吸収が進む状況を作れていることが大前提であることを理解していただきたいのです。
<ゾーン②>装置の除熱性能が主役のゾーン(熱移動律速)
液温が運転温度上限付近までくると、 これ以上の温度上昇を回避するために、 ジャケットやコイルの冷却能力を増大させて設定運転温度を保持します。 その後、 その冷却能力が最大限になると、 今度は水素の供給量を絞ることで反応速度の調整を行い、 液温上昇を回避します。
よって、 このゾーンでは、 反応速度に応じて発生する反応熱の除去能力が律速となるので、 予めコイルやジャケット等を設置することや伝熱性能の高い撹拌翼の選定等が重要になります。
「もっと除熱能力の高い設備なら、 反応速度を上げて運転時間を短縮できるのに残念だ」という現場オペレータの声は、 このゾーンの話をしているのです。
<ゾーン③>ガス巻き込み性能が主役のゾーン(巻き込み量律速)
ここでは、 ポリマー中の二重結合の数がかなり少なくなり、 液中の水素イオンとの会合・反応の機会が大きく減少することで、 液中水素イオンの消費が低下して、 供給される水素が液中へ溶解する前に自由液面からガス相へ吹き抜ける現象が起こります。 その結果、 ガス相の圧力が増大して液相を押すことで系内全体の圧力が上がってきます。 系内の圧力増加は、 ヘンリーの法則により液中の飽和溶存水素量を増大させるので、 気液間のガス濃度勾配が上がることになり、 ガス吸収速度は向上します。 しかし、 缶内上限圧力まで到達してしまうと、 これ以上にガスを系内へ押し込むことができなくなり、 水素ガスの供給が停止してしまうのです。 そうなると、 液の自由界面からの気相部ガスの再巻き込みを待って、 系内の圧力低下に見合った極少量のガスだけしか系内へ供給できなくなるのです。
図10に同一単位動力(Pv=1.0kW/m3)での撹拌翼種による巻き込み性能比較を示します。 通常、 処理量が増大すれば運転時間は増大しますが、 図11からも分かるように、 撹拌翼の種類や除熱性能の向上(コイル増強等含む)による最適化を行うことで、 処理量増大(1m3⇒3m3)でのスケールアップでも大幅な生産性の改善が可能となるのです。
「運転の後半は、 気相部からのガス巻き込みが弱いから、 槽内の圧力が下がってくれない。 ガスを吹き込むことができないので、 どうしようもない。 ただ、 じっと待つばかり。」というオペレータの話は、 実はこのゾーンの声なのでした。
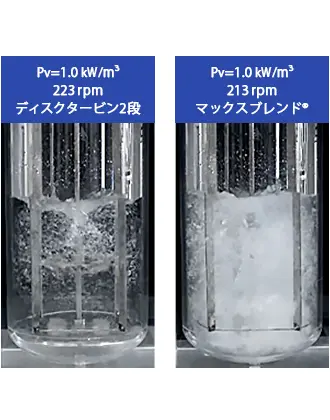
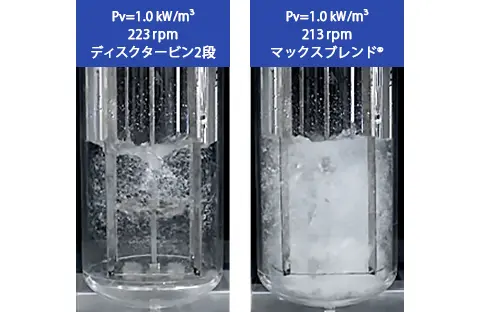
巻き込み状況の比較(4枚バッフル有)
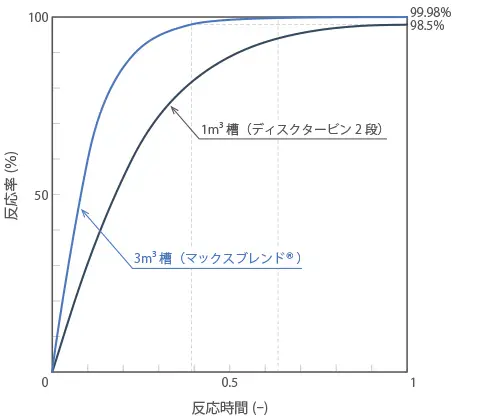
(1m3槽から3m3槽へのスケールアップ)
以上、 一般的な水素化工程での1枚の運転チャートではありますが、 バッチ運転であるがゆえに、 その運転過程で反応を進行させる機能の主役が大きく変化することをご理解いただけたかと思います。
-
なるほど、たしかに水添槽は、単位操作のオンパレードだ!
-
運転中に変化する主役機能を、最大限に活躍させる生産処方が決め手なのですね。
これからも、触媒を制する者は、化学を制するのか?
本編では、 水素化工程を3ゾーンに分けて、 ①物質移動→②熱移動→③再巻き込みと各々の主役機能を紹介しました。
さてさて、 主役はこの3人だけで大丈夫なのでしょうか。 前述の3機能は、 物質や熱の移動現象をベースにした評価でしたが、 水素化ではポリマー分子構造への選択的な水素イオンの結合反応が伴うので、 そこでの重要な機能として「触媒の効用」が出てくるのです。 化学会社の研究員の皆さんの声をいくつか紹介しましょう。
-
ポリマー分子配列内の二重結合へ選択的に水素イオンを結合させる触媒開発が大変。
-
触媒の効能を長時間発揮できる長寿命触媒の調査・探索が難しかった(特許絡みもある)。
-
混合&伝熱性能の高い撹拌槽採用で、触媒の追添を無くせたのは嬉しかった。
(触媒追添には、槽内の高圧水素の脱圧が必要で結構、手間がかかるので。) -
使用済み触媒の、ろ過・分離・回収プロセスも各社の重要なノウハウだ。
-
混合性能の良さが、短寿命触媒の使用時に有効に働くことを実感できた。
逆に、同一触媒条件での反応速度の違いで撹拌翼の混合性能を評価できた。
古くから、 「3C(自社、 顧客、 競合)だけでなく、 追加の2C(顧客の顧客、 顧客の競合)も加えた5Cの変化をちゃんと意識せよ」と言われたものです。 この5Cの動きを、 日頃から常にアンテナを高めて意識する姿勢があれば、 顧客が飛びつく商品化のアイデアは、 おのずと浮かんでくるのかもしれませんね。
「顧客の立場に立つ」ということは、 顧客がいる環境(顧客の顧客、 顧客の競合)を知ることから始まるのではないでしょうか。
- 撹拌講座 初級コース
-
- はじめに 撹拌の基礎用語
- その1 基礎の基礎、 撹拌を理解する3つのポイント
- その2 「撹拌の目的」の具体例
- その3 「粘り気」の単位が粘度
- その4 撹拌槽を巨大な粘度計と考えてみよう
- その5 動力変化で流れが見えますか(前編)
- その6 動力変化で流れが見えますか(後編)
- その7 撹拌Re数の本質を知ろう
- その8 スケールアップの基礎の基礎
- その9 スケールアップの基礎
- その10 撹拌槽の伝熱性能とは?
- その11 槽内側境膜伝熱係数hiとは?
- その12 撹拌講座の総括