Professionalism Troubleshooting Tackled by All Sumitomo Heavy Industries ~ Turning trouble into a trigger for improvement. In-depth approach to stable operation of the device. ~
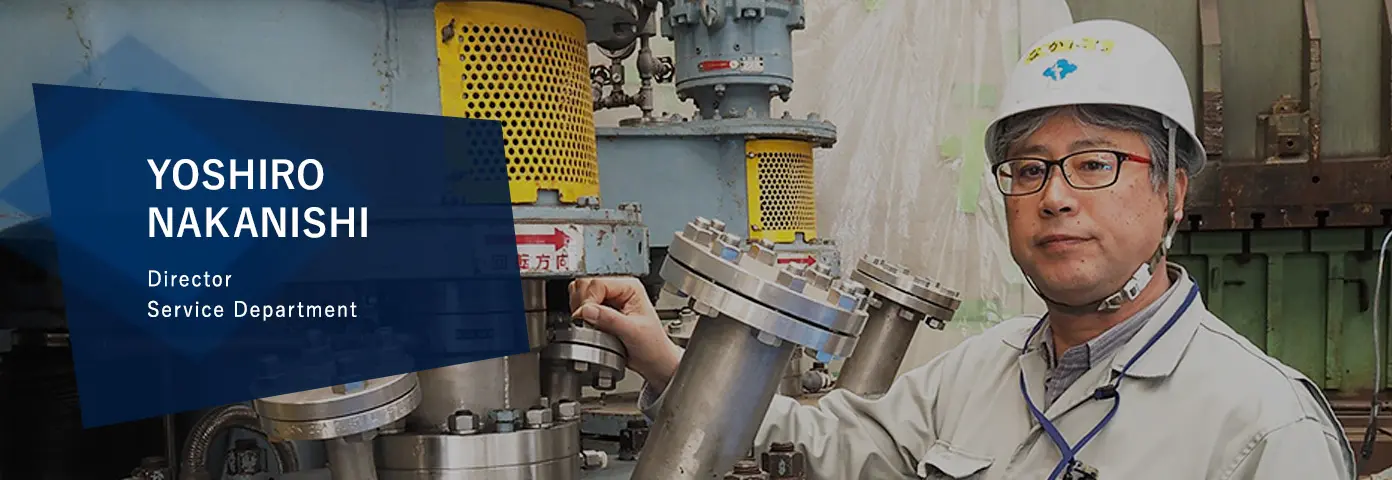
After-sales Service
Sumitomo's mixing vessels operate all over the world. Mr. Nakanishi, Manufacturing Department, is one of our professionals who support the stable operation of the devices after delivery to our customers.
Mixing devices for our customer's manufacturing process. We interviewed Mr. Nakanishi about his experience with device troubleshooting. What does he do to further improve our customer's equipment when an issue arises?
How do you approach troubleshooting for a mixing device?
In addition to high-performance mixing impellers such as MAXBLEND and SUPERBLEND, our company has worked on tanks of mixing devices for many years in the pressure vessel business. Also, since our Group companies are manufacturing motors and speed reducers that power the devices, we are able to respond flexibly to the tasks from device development to troubleshooting after the delivery of devices. This is, as a Group, we have comprehensive knowledge about the agitators, which is different from those manufacturers specialized in impellers and tanks and our unique strength.
Furthermore, collaborating with technical research institutes of Sumitomo Heavy Industries and universities allows us to discover the root causes of issues through advanced chemical analysis.
Versatility combining the power of the Group, which is the strength of Sumitomo Heavy Industries, is also effective in troubleshooting. Please tell us about specific troubleshooting cases.
Troubleshooting Case 1:
Contents leaking due to stress corrosion cracking in stainless steel
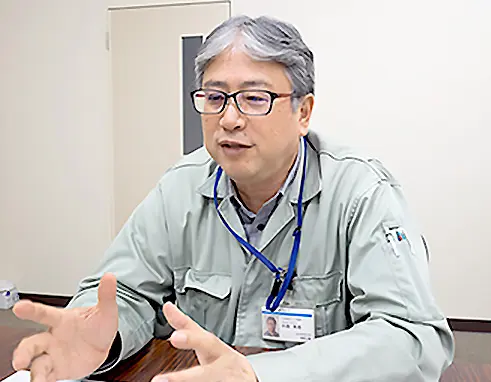
First, let me provide an example of Company A, which I experienced in 2013. It is a situation called stress corrosion cracking (SCC). This is an issue that chemical manufacturers worry about a lot. Although it is rare because of limited occurrence conditions, corrosion cracking will progress rapidly and the risk of hazardous substance spillage will increase depending on the material used.
How does it occur?
Generally, material factors (stainless steel), stress factors (tensile stress due to high temperature) and environmental factors (chlorine, in this case) are involved. SCC occurs when the three conditions are met. We rushed to the site in response to a call from the customer notifying us of the leakage, but we did not immediately determine that it was caused by SCC.
However, the customer worried a lot and was puzzled as to why it leaked through extremely thick steel material only 4 or 5 years after starting operation. With priority given to restarting the operation, we replaced all the relevant parts.
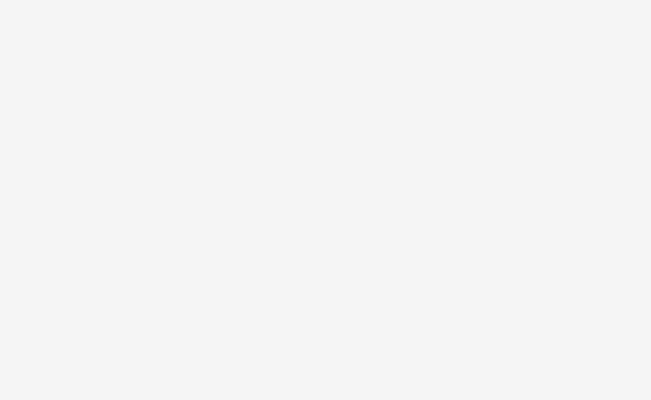
Then you started investigating.
Yes, we did. We cannot decide how to address a problem unless we know the cause, so we decided to cut out a portion where the crack occurred and bring it to our laboratory. We used Electron Probe Micro-Analyzer (EMPA) analysis on the stainless steel structure and found high chlorine concentration in the cracked portion, which is characteristic of SCC.
However, we had the big question: No chlorine-containing raw materials were used during the process in which the issue occurred. We decided to persistently find the root cause of the SCC together with the customer. It became evident that the chemicals used for washing the mixing vessel were suspicious. We found that this chemical contained trace amounts of chlorine.
After a three-month investigation, we finally discovered that small amounts of chlorine remained in the liquid pool of the nozzle at the lower part of the mixing vessel because the chemical used for washing was insufficient, and it gradually became condensed as the temperature increased and decreased, resulting in SCC.
We suggested maintenance of the containers to the customer so that the chlorine concentration will not continue to progress. Now it has been in stable operation.
By tirelessly investigating, you discovered a cause that you did not even imagine.
That is correct. I have worked in this industry for more than 30 years, but I realized that there are many more things to learn. I am working hard and learning every day.
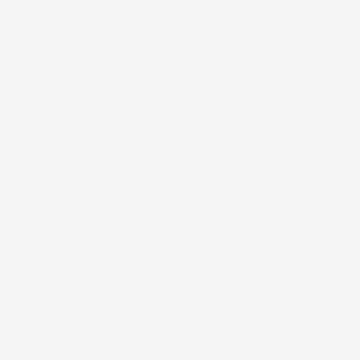
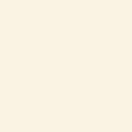
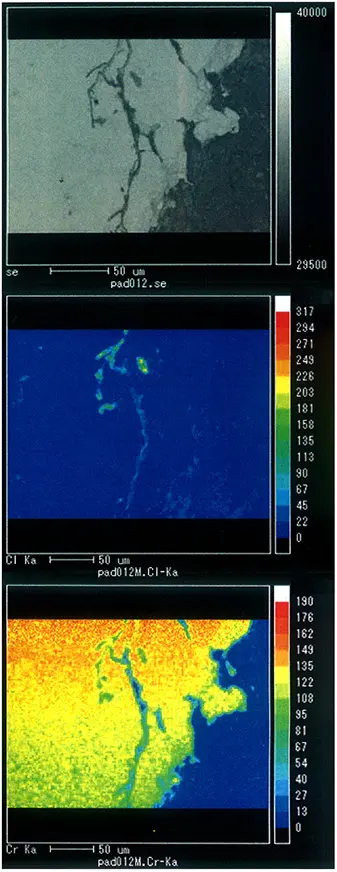
Relationship between SCC and chlorine concentration
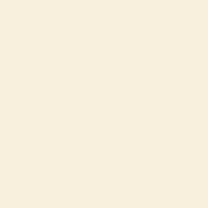
Troubleshooting Case 2:
Bearing failure of a large speed reducer
Another example that I would like to introduce is about the mixing vessel delivered to a factory in China of Company B, a chemical manufacturer. It was a very large mixing device with a large speed reducer and a driving motor capacity of 710 kW installed. However, this is an issue where the speed reducer's intermediate shaft, which should be quite robust, was damaged due to the output shaft bearing. The Φ 300 mm shaft was damaged only 1.5 years since it started operation. The customer, of course, and we also were very surprised by these findings.
If it were a standard product, it would be possible to extrapolate the cause to some extent based on past issues. Since it was the speed reducer of special order size, it was difficult to find the cause. We brought the damaged parts back to Japan and used trial and error by conducting organizational analysis and examining the cross section, with the cooperation of the Group companies which was in charge of production. We requested that a university professor take a look at the analysis results and teach us the mechanism that caused the damage, and then we finally discovered the cause.
Actually, we found that less than 1 mm of foreign matter got into the lubricating oil of the speed reducer, which was bitten by the bearing, causing indentation. Uneven areas formed in the stress state inside the material, resulting in a fatigue fracture. We presented the analysis image of a Scanning Electron Microscope (SEM) to the customer to explain that the metal structure broke due to fatigue. We also suggested that the customer take measures to prevent contamination from foreign matter, such as using fine filters so that foreign matter does not get mixed in when adding lubricating oil for maintenance.
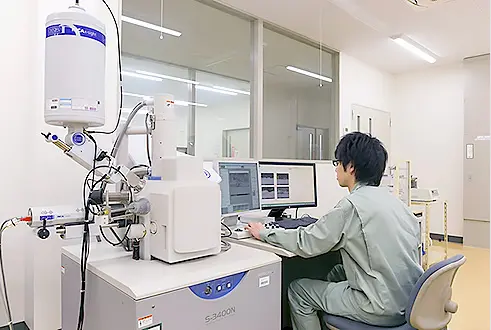
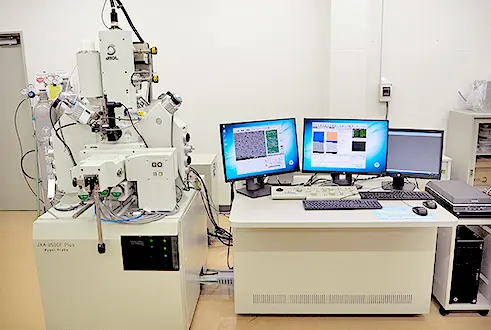
While the previous case was settled in 3 months, how long did it take this time?
For this issue, first we exchanged the shaft to resume operating, and then started investigating it. However, as it was an issue that occurred 1.5 years since the start of operation, the customer was very concerned about the possibility of a recurrence. We worked as quickly as possible and were able to solve it in about 2 months, even though the issue had occurred abroad.
It seems to me that Case 1 and 2 are sophisticated approaches such as scientific investigation.
That is a good point. It is scientific investigation itself. There is a part that forms the starting point of the beginning of breakage in everything. It is important to persistently investigate the starting point.
Our Group companies' Yokosuka and Niihama laboratories in Japan have great strengths in materials chemistry as a heavy industries company. We are able to respond quickly to tasks ranging from component analysis to macro structure observation. Since our company has a good relationship with universities in Japan, I think that problem solving with such an analytical approach can is a big advantage compared with competitors. In addition, since we have worked on nuclear reactors in the past, we have an abundant accumulation of knowhow for troubleshooting with regard to welding and materials, and we are still pretty good at it.
After solving the issue, the operation of the equipment stabilized and the maintenance cost decreased.
I am trying to arrive at such a solution.
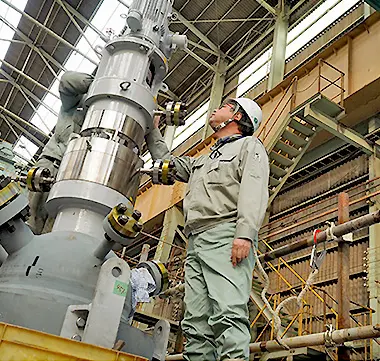
Besides these scientific approaches, what do you usually keep in mind?
Although I have experienced troubleshooting in a variety of cases, since all the mixing devices we work on are basically custom made, the troubles are all different. As I said earlier, although the standard product has some clues as to how to deal with it, custom-made products are not easy. For example, looking at one issue, such as heating medium spill from a jacket, first you still have go to the customer, because you will not understand the situation unless you actually see it. Also, the longer the process is stopped, the greater the customer's loss, so it is also necessary to restore operation as soon as possible. In that sense, it is important to have "three-principles" in which go to the actual place(genba), see the actual product (genbutsu),and know the actual situation(genjitsu).
Another thing I keep in mind is not only eliminating the cause of the issue, but also making proposals tailored to the operating conditions specific to the customer's equipment. If you can go the extra mile to find the optimum customization for the customer's equipment, you will be able to offer better solutions that lead to easy maintenance, lower operating costs and so on. By looking at the issue as an opportunity, we will be able to help extend the lifetime of the customer's equipment.
The idea of eliminating a risk to stable operation triggered by an issue is very positive thinking. Lastly, what is the best part of this work?
In a situation where the equipment stopped and production was halted, even though the cause of the issue is not related to our company, we often get scolded by the customer as soon as we arrive, "What on earth is going on?"
In any situation, we make every effort to resolve issues for our customers and seek a solution as quickly as possible. Sometimes it may take several months, but I try to do my best. Alongside the customer, seek a tailor-made solution and make them happy. Because of that experience, I have been able to continue with this work, which is the real pleasure of this work. If you try hard, you can be happier, right?
I hope to continue working on troubleshooting as anticipated by our customers who say, "That's Sumitomo Heavy Industries as expected."
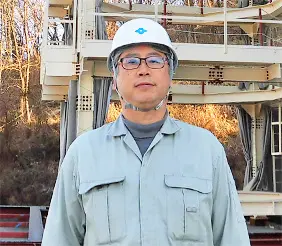
Our professionals
Mr. Yoshiro Nakanishi
Sumitomo Heavy Industries Process Equipment Co., Ltd.
Director
Service Department
Joined the Company in 1982.
Majored in Mechanical Engineering at university.
Through many years in various departments, such as design, technology, construction, and quality control, he has worked on a wide variety of mechanical structures, including oil drilling rigs and marine structures, caissons of the Honshu-Shikoku Bridges, bridges, coke oven machines, and mixing devices. Currently, as director of the Manufacturing Department, he has been busy travelling around Asia, including China, South Korea, Thailand, and Japan. His hobby is road cycling.