Mixing Vessels Useful Clues for the Mixing Beginners Mixing Course
- HOME
- Products & Solutions
- Mixing Vessels
- Mixing Course
- Beginner course 12:Mixing course review
Course 12
Mixing course review
This is the summary of the 11 sessions of the beginners' mixing course. Thank you for reading.
Through this beginners' course, we most wanted to impart, as mentioned in the first session, what mixing devices are. As you can suppose from names such as a juicer mixer and a washing machine, it is not named after the purpose (WHAT) of the person who uses it, it is named as a means (HOW).
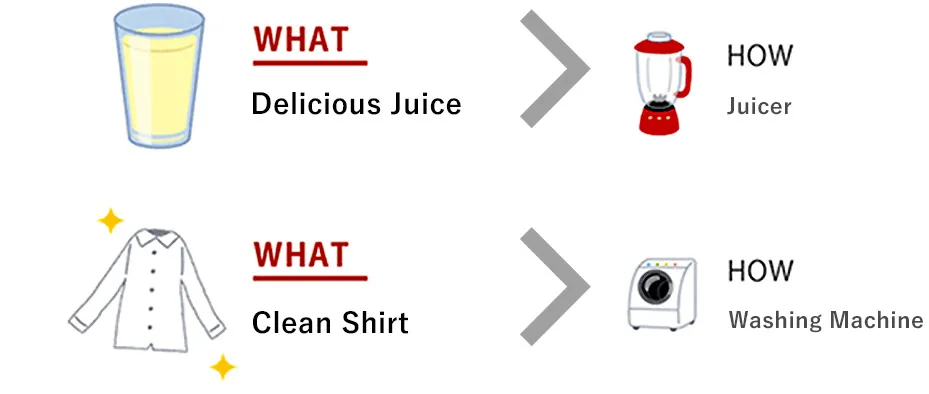
What is known as a mixing device in the industry has a variety of purposes (WHAT), for example, dissolving powder (Dissolving tank), precipitating crystals (Crystallizer), obtaining an emulsion (Emulsion tank), or adding hydrogen to polymers (Hydrogenation reactor) and so on. Anyone who manufactures a mixing device and uses it will be able to discuss how to use (HOW) the mixing device for the first time by properly recognizing and identifying the WHAT.
However, there are also some places where it cannot be said that current mixing technology can accurately express the degree of influence on all unit operations for such conditions that WHATs may proceed at the same time, physical property change during operation and scale-up with non-Newtonian fluid.This is why mixing is said to be difficult, that the empirical formula is full of experimental results, or that it is a difficult science to be organized. Also, that is why a large number of pepole gather at lecture meetings with the theme of mixing technology and scale-up.
When preparing for this course, we wondered how to summarize mixing, but first we decided to list keywords (memorable phrases) for each session. It's like a contents table from previous sessions, but it can be easier to understand the points of mixing.
Reviewing the mixing course for beginners.
-
- What do you want to mix? Mixing is a means. What is your purpose for mixing?
- Know the characteristics (physical properties) and the change of material to be mixed.
- Liquid flow is a good balance of impeller, vessel and internals.
-
- Unit operations that take place inside of a mixing vessel.
Identify critical unit operations from countless choices.
Identify the objectives, functions and factors that lead to improved quality and productivity.
- Unit operations that take place inside of a mixing vessel.
-
- The apparent viscosity of non-Newtonian fluid changes with the shear rate (impeller rotating speed).
-
- A mixing vessel is a huge rotating viscometer. An impeller is a rotor for a viscometer.
- Operation data (rotating speed and power) of a mixing vessel can indicate the flow condition.
-
- The mixing power consumption change during operation can provide an idea of the viscosity change in a vessel.
-
- The factors affecting mixing power differ between turbulent and laminar flow. Also, attention should be paid to the presence or absence of baffle plates.
-
- Is the mixing Reynolds number expressing the degree of disturbance in the entire vessel?
- MAXBLEND can be regarded as the ultimate infinite stage paddle impeller.
-
- Scale-up for a mixing vessel is like a huge okonomiyaki. How do you like it?
-
- Three vital points for scaling up:
Have scale-down data for the actual expected size during the phases of laboratory testing.
Scale-up at a constant rotating speed in a turbulent region involves excessive power, which is ridiculous.
Imagine the function that you want to maintain before and after scaling up.
- Three vital points for scaling up:
-
- The heat transfer capability can be determined by multiplying the heat transfer area by the U value and the temperature difference.
- The temperature difference is determined according to the operation, and heat transfer area × U value will yield the device characteristics.
- Heat transfer coil enhancement is a trade-off with uniformity in a vessel.
- U value is like skewered oden. Mixing conditions only affect vessel inner film heat transfer coefficients.
-
- For improving U values, among the five factors, a factor that has a large heat transfer resistance should be improved. In a turbulent region, the metal resistance of the vessel wall may be rate limiting, so special care is required.
- Improving vessel inner film heat transfer coefficients and U values by increasing rotating speed is less effective than increasing mixing power.
- Film heat transfer coefficients greatly vary depending not only on the viscosity but also on the thermal conductivity and the specific heat.
Although these are provided in short sentences, each item has a deeper meaning when applied to mixing technology. If any keyword interests you, go back and read the previous lectures.
In this course, you also learned about various dimensionless numbers. Although they are useful indicators for scale-up where size changes because there is no dimension of length, they may create difficulty when determining the characteristic length and speed.
In addition to an explanation in each session, we provided a figure to see the changes to each factor before and after the scale-up using two patterns: turbulent and laminar flow. We also provided a list of methods for calculating the degree of change in Appendix - 1 and Appendix - 2. Try to imagine how the characteristic value changes with each scale-up method.
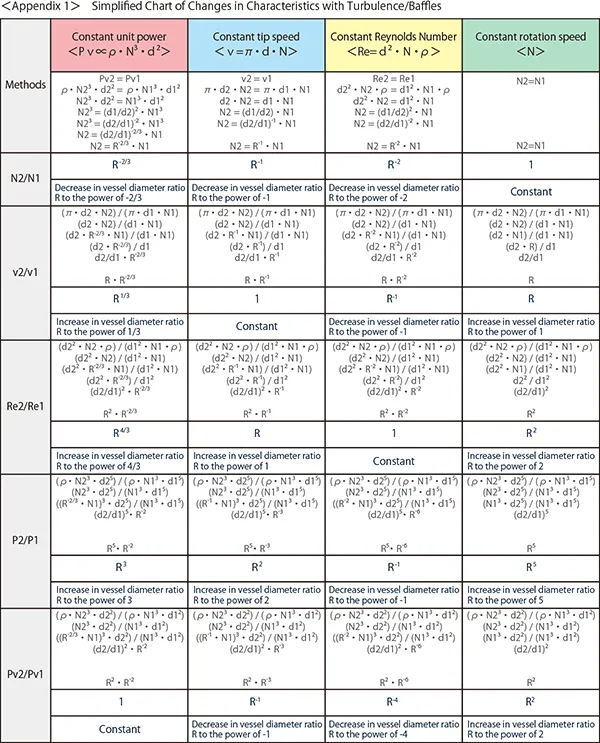
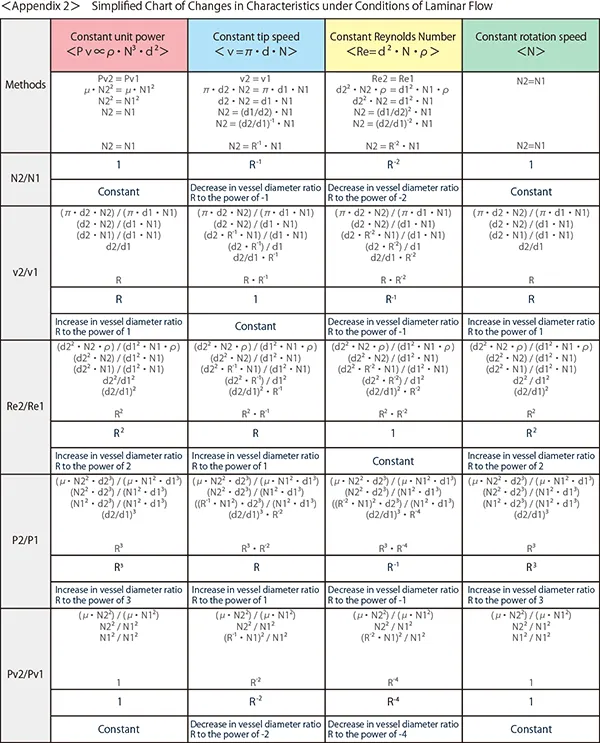
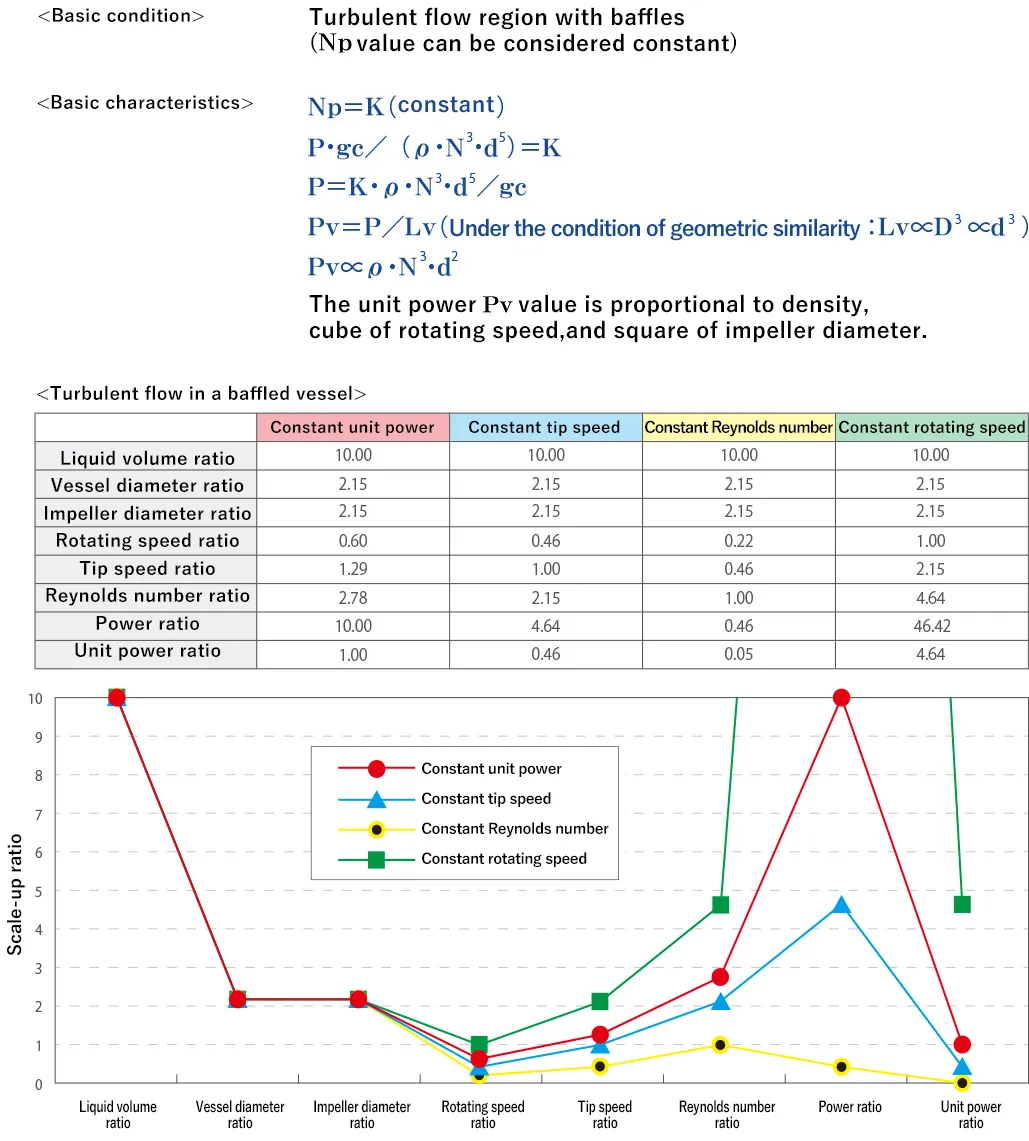
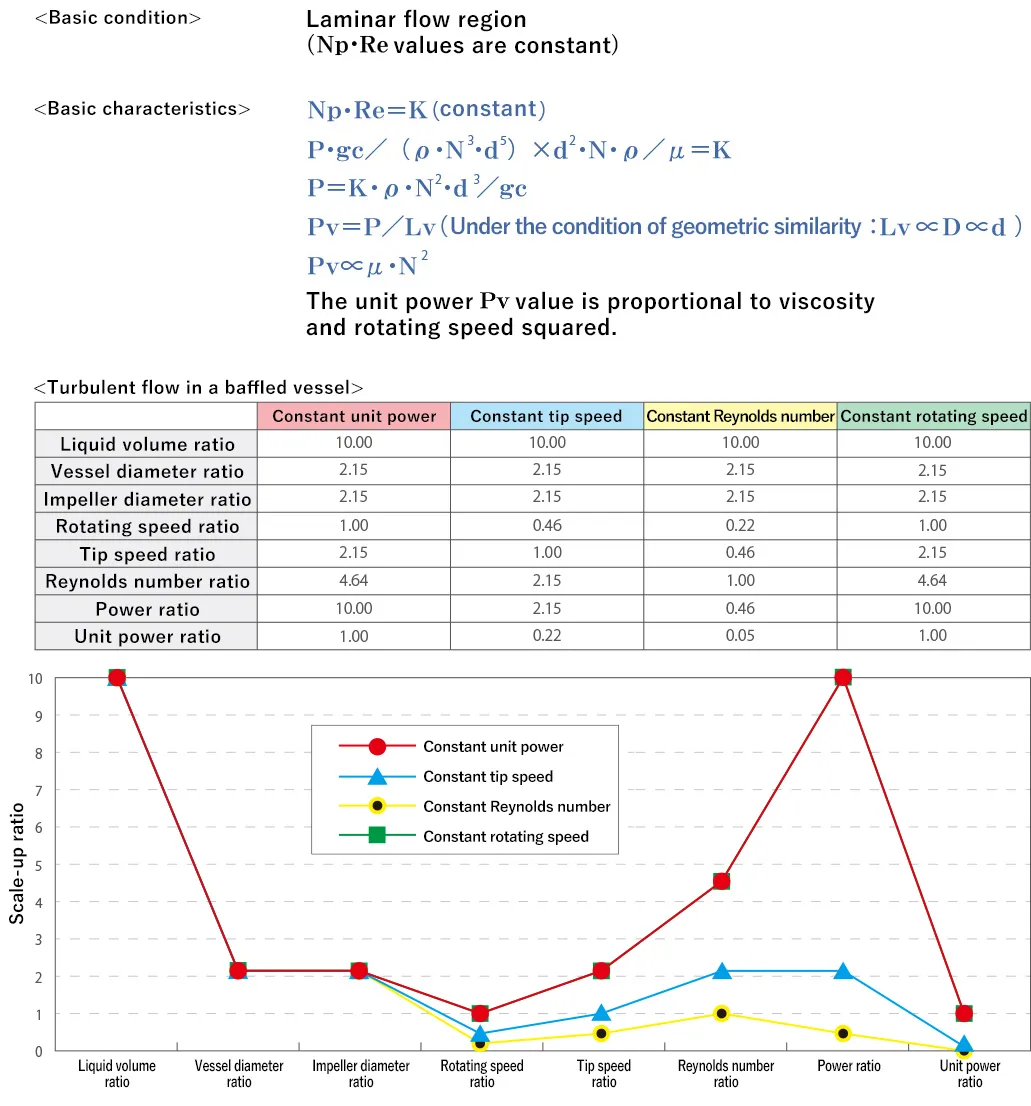
To wrap up the beginners' course, we prepared the following exercises as a final exam. It may be too easy for those of you who studied hard throughout this course, but give it a try.
Give it a try! Taking the final exam for the Beginners' Course.
- (1) Provide characteristic length and speed in Reynolds number for a pipe flow and mixing vessels, respectively.
Also, describe the difference in the physical meaning of each Reynolds number. - (2) You are assigned to analyze a mixing vessel with 3-stage 4-pitched paddle impellers.
You immediately tried to calculate the Reynolds number for the vessel, but the impeller diameter is different for each of 3-stage paddle impellers.
What is the best characteristic length when calculating the Reynolds number for this mixing vessel? Describe your reasoning. - (3) Suppose you are asked by a production staff that it may be necessary to increase the rotating speed slightly, which is currently set at 40 rpm, because the product properties are not stable.
How high can rotating speed be increased? When you need to provide a prompt answer for the maximum rotating speed at site, describe what information about the mixing vessel is needed and what kind of answer is appropriate. - (4) When planning retrofitting to increase the motor power rating by one rank in order to increase the mixing intensity of existing agitator, provide at least two examples of what should be considered in terms of agitator mechanical strength.
- (5) Suppose a pilot product with a liquid volume of 200 L was successfully made at a rotation speed of 100 rpm (Pv = 1 kW/m3). When planning to manufacture a geometrically similar mixing vessel with a capacity of 10 m3 by scaling up at a constant unit power, calculate the motor rating and design rotational speed.
Provide the flow state in a vessel under the two conditions shown below:
Case 1: Turbulent flow in a baffled vessel
Case 2: Laminar flow
-
Click here for
sample answers.
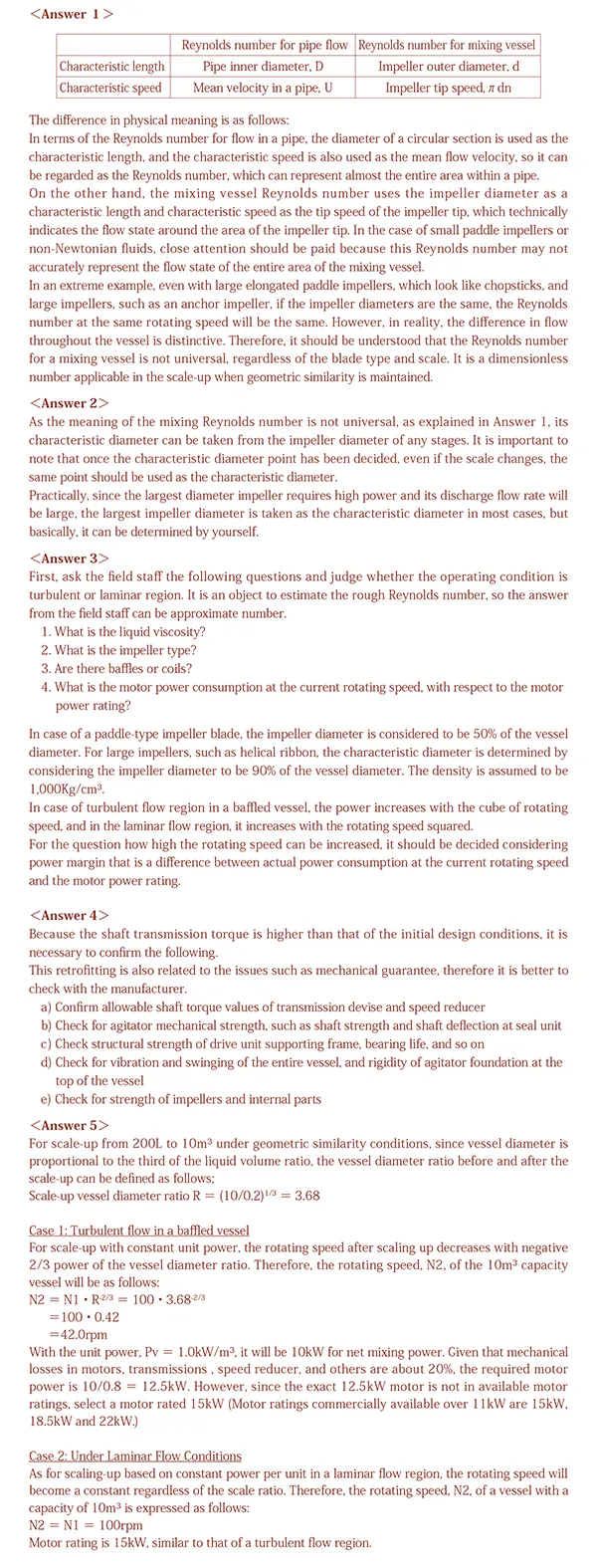
Beginners' course review
Allow me to introduce the words of my university professor 30 years ago. When I was a student, I half-listened to my professor, saying "Uhh?" Now I realize that it is very important when working as an engineer in a company. In previous sessions, I mentioned that scaling up of a mixing vessel is 60% theory, 20% courage, and 20% luck. We received a pep-talk from some customers who said, "What kind of mixing vessel manufacturer are you, saying luck and courage are 40% of a mixing vessel? Work harder!" We wanted to impart that this courage and luck are not simply reckless behavior; they are the result of a specific hypothesis (decision) and accuracy from individual engineers.
In other words, since you are young, if you make a lot of decisions, experience a lot of mistakes, and acquire some necessary cruces (vital points), the courage and luck will remain in your mind as an engineer. That is what we meant to say.
Engineers working for a company have an obligation to fulfill the QCD (quality, cost and delivery) for the assigned work. Time is limited and you cannot discuss armchair theories for hours. The mission of engineering is to finish better quality products within the planned budget and schedule.
It may be said that the ideal service is "Anytime, anywhere, to everyone," as with one-click shopping, but Japanese-style hospitality is said to be "only now, only here, only you." At Sumitomo Heavy Industries Process Equipment, we would like to continue to be a company that can provide technical hospitality to our customers and looking forward to working with you.
Engineering is decision making!
The difference between science and engineering is that while the former aims to understand, the latter aims to decide.
In engineering, deciding is more important than understanding so in an extreme case, a decision may be made without understanding.
However, another role of engineering is to make effort to decide as reasonably as possible.
Deciding is decision making. In chemical engineering, decision making can be roughly classified into three phases:
1. research and development,
2. planning/design,
and 3. operation/management.
In phase 1, abstract decision making is required because uncertainty is large.
In phase 3, there is little uncertainty and very specific decision making is required.
Phase 2 is halfway between them.
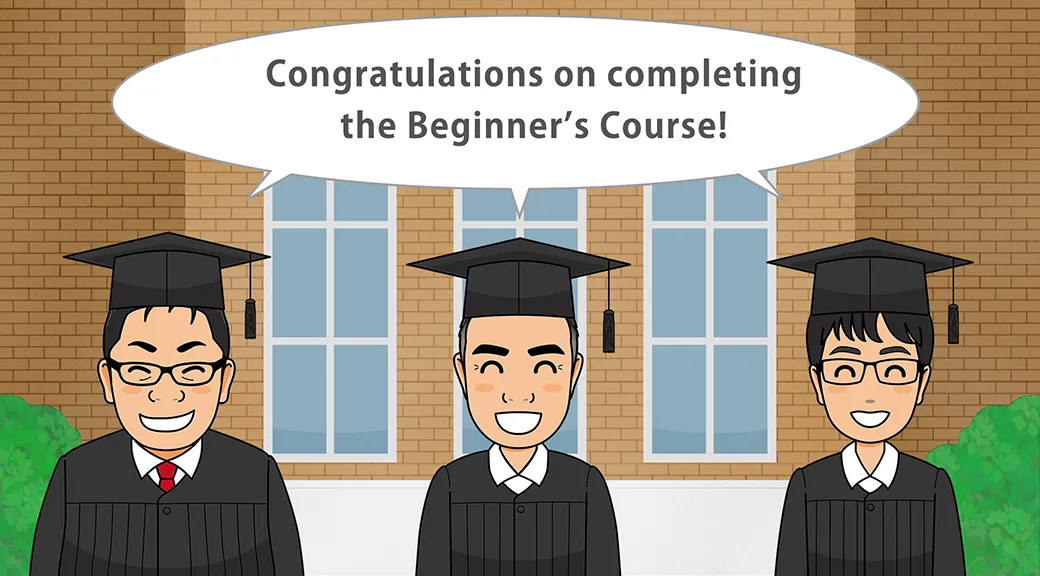
-
Mixing Course
Beginner
course -
- Introduction Basic terms of mixing
- Course 1 Basics of basics: Three points to understand mixing
- Course 2 Examples of the purposes of mixing
- Course 3 Viscosity is the unit of stickiness
- Course 4 Consider a mixing vessel as a huge viscometer
- Course 5 Can you see the flow from power change? (Part 1)
- Course 6 Can you see the flow from power change? (Part 2)
- Course 7 Learn the essence of the mixing Reynolds number
- Course 8 Basics of basics of scaling up
- Course 9 Basics of scaling up
- Course 10 What is heat transfer performance in a mixing vessel?
- Course 11 What is film heat transfer coefficient , hi?
- Course 12 Mixing course review
-
Mixing Course
Practical
course -
- Introduction Mixing course SEASON II
- Course 1 Immediately determine the basic specifications of the mixing vessel using three pieces of information: operating liquid volume, viscosity and density.
- Course 2 Find a plan to improve the productivity of the mixing tank on the existing production line! (Part 1)